PLAST-CONTROL: New “Pro Clean” and “Pro Drain” gravimetric systems
Automatic emptying and cleaning of suction feeders and gravimetric metering units
BACKGROUND
Abrasion, dust or angel hair (due to static, among other things) settles in all hoppers and system parts that come into contact with granulates. In addition, depending on the design, there are so-called “dead zones” in which the undesirable substances can accumulate.
These impurities have a negative effect on production after a change of material or after an undefinable period of time (sudden loosening of an accumulation): inclusions, holes, streaks or colour variations are the result. The film produced is then usually unusable.
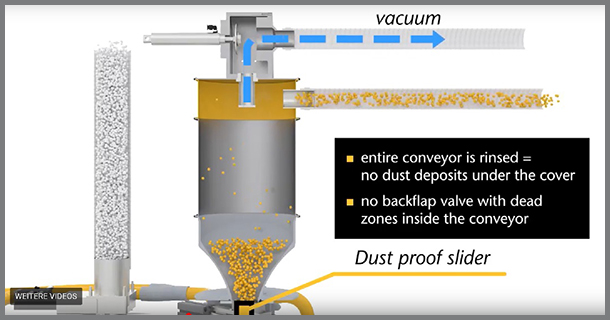
Suction of the material, separator has slide instead of free-falling flap – advantage: no “dead zones” due to the free-falling flap!
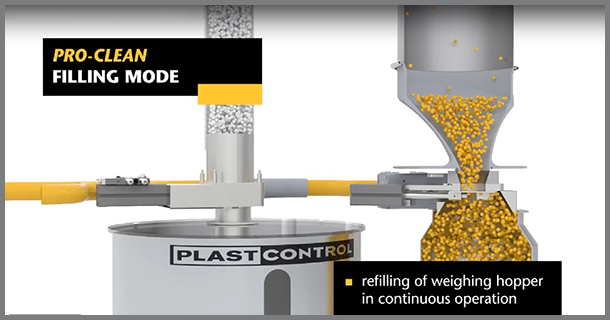
Weighing hopper is completely filled – advantage: Deposits due to static on the hopper wall are avoided!
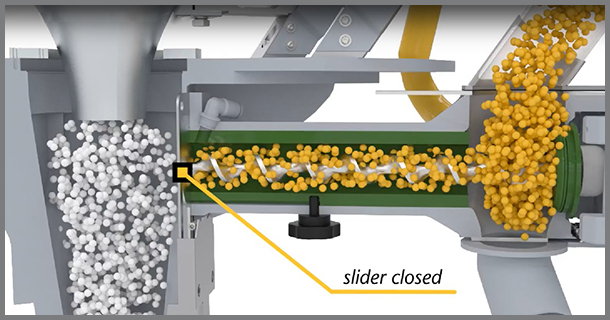
Material flow of the metering unit has a slide valve – advantage: Material does not fall further into the main material flow!
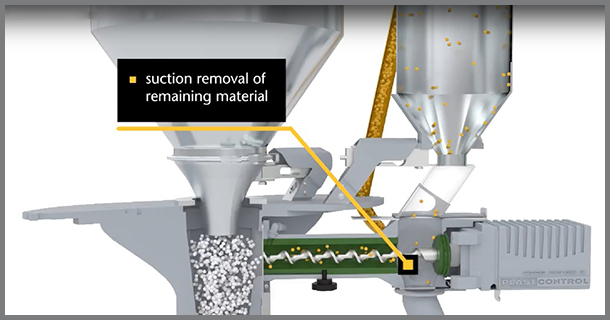
Material is sucked out of the component – advantage: No manual emptying necessary, significantly shorter changeover times!
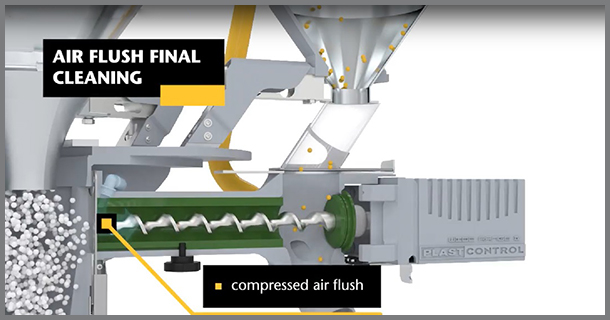
Component is cleaned with blasts of compressed air
Advantage: Complete cleaning of the component from dust and granulate residues!
MATERIAL CHANGE
At the end of a job, many conveyers and material storage containers are still well filled and, in the worst case, have to be drained and cleaned manually before new material can be filled in. This process, which is necessary during a production changeover, causes waste and costs valuable machine time. This process can only be shortened by using an intelligent suction conveying control such as the MMC (Material Minimizing Control) from PLAST-CONTROL.
„PRO-CLEAN“
“PRO-CLEAN” essentially consists of a new mechanical design of suction conveying and continuously operating gravimetric separators to prevent contamination and deposition of unwanted materials such as dust, granules and angel hair. The separators have a new design without a “free-fall flap” (always an area for “dead zones”). The vacuum required for the conveying process is built up against a dust-tight gravimetric slide; the “free-fall flap” is omitted.
In addition, the material inlet into the separator has been redesigned (previously also an area for “dead zones”); due to a lateral arrangement, the material flows into the separator in a tangential direction and cleans off this area; the non-return flap is omitted.
The gravimetric hopper is now completely filled and, due to the conical design, all inner hopper surfaces are continuously cleaned by flowing granulates and dust or granulates are prevented from sticking to the walls.
„PRO-DRAIN”
“PRO-DRAIN” is probably the most comprehensive solution on the market for automatic cleaning and extraction of materials during product changes on extrusion lines.
In connection with “PRO-DRAIN”, the intelligent suction conveying control MMC is always installed. The operator specifies an order length to the system and MMC sucks in only the material required for it and ensures that at the end of the order the hoppers are empty except for a safety residue. MMC only controls the secondary components (!!!), the main component remains unaffected.
As soon as there is enough material in the gravimetrically weighed hoppers to complete the job, the operator is informed by MMC that the material line can be cleaned. The system cleans the material line via free-suction valves. The next step is to clean the separator from the inside via compressed air shocks; the material slide opens for the last time and discharges the residual material into the gravimetrically weighed hopper. From now on, the operator can already suck in new material needed for the next job.
When the job is completed, the next step is to stop the feeder and close it against the main material flow via a pneumatic slide. The metering motor slowly rotates backwards and the material still present in the metering unit and gravimetric hopper is sucked out via an external suction conveyor. In addition, any remaining granulate in the feeder and hopper is loosened via compressed air blasts and also sucked out.
There are 3 different processes available to the operator for cleaning with compressed air blasts.
- Clean the separator and the gravitational drive at the same time with compressed air and suction.
- Clean only the separator with compressed air.
- Clean only the gravimetric system with compressed air and suction (the slide to the separator remains closed because new material has already been sucked in).